From Lab to Patient - How to Ensure a Successful NPI Launch
Catherine Taylor
Communication & Content Manager
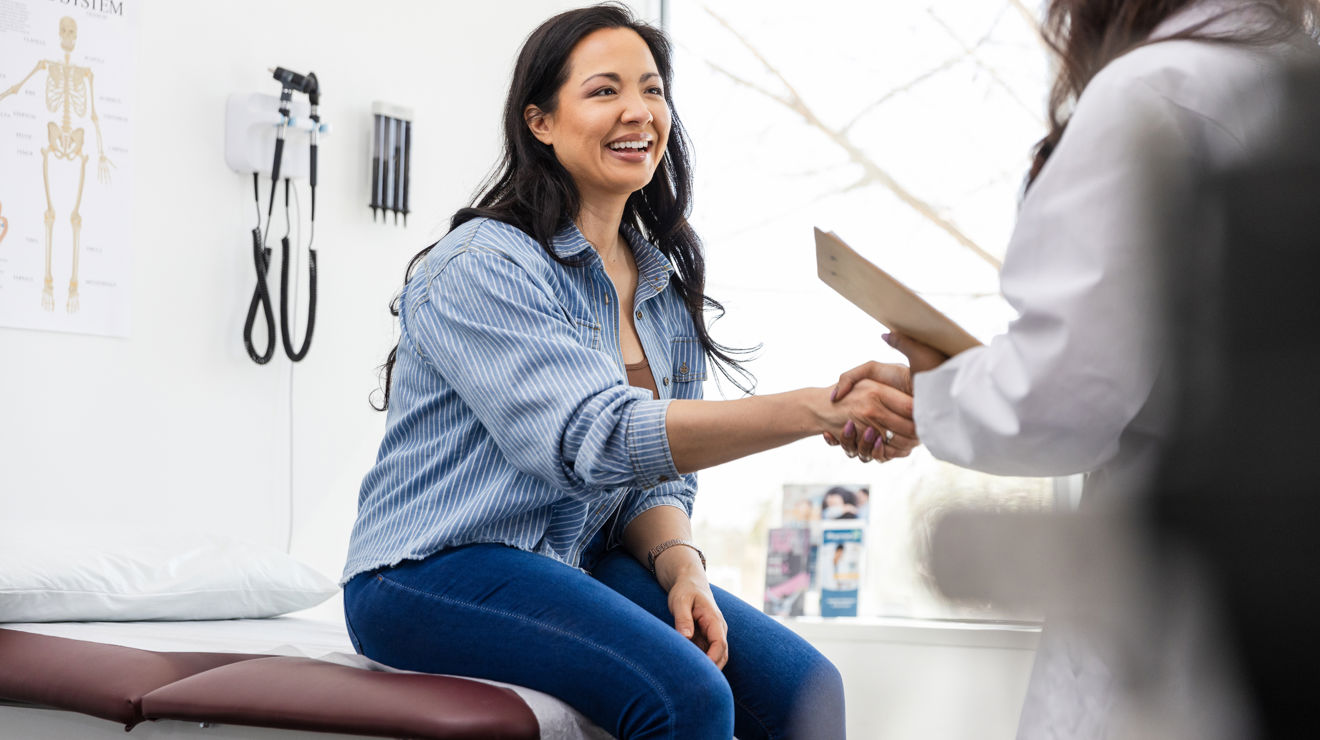
Launching a new pharmaceutical product, known as a New Product Introduction (NPI), is filled with complexities and risks. The pharmaceutical industry faces unprecedented challenges, including strict regulatory demands, unpredictable approval timelines, and heightened market competition.
But a successful NPI launch is not just about meeting business objectives; it’s about advancing therapies and offering new life-saving medications to patients who need them.
The stakes are high, and any delays or damaged batches can jeopardize the entire product launch, potentially causing significant repercussions for the company and patients. According to a 2024 report by IQVIA1, the global pharmaceutical market is expected to grow at a compound annual growth rate (CAGR) of 5-8% from 2024 to 2028, reaching around $2.3 trillion. This growth underscores the importance of meticulous planning and execution in NPIs.
7 Steps to Protect Your NPI Launch
1. Assess the Product Risk Profile
A risk management approach is essential for the NPI process. Assessing the product’s risk profile helps determine the logistics solution and associated costs.
- Temperature Range: Identify the product’s required temperature range.
- Sensitivity: Determine if the product is sensitive to high or low temperatures and determine the degree of its sensitivity.
- Storage: Assess if it can be stored long-term in a chilled warehouse or temperature-controlled container.
These factors will all be important when deciding and qualifying your packaging solution to ensure that the quality and efficacy of your product is protected during transportation.
2. Determine the Appropriate Mode of Transportation
After establishing product requirements, the next step is to plan the transportation. You should choose the transportation method that ensures the product reaches its destination without damage or degradation to product quality.
- Air Transport: This is the preferred transportation method for NPIs due to speed, reliability, and control.
- Ocean Freight: This can be less expensive for intercontinental bulk transport but is slower with potentially increased levels of risk.
Selecting the right mode of transportation is critical to maintaining the product’s integrity and meeting tight deadlines.
3. Select the Right Packaging Solution
Temperature excursions are the primary cause of degraded pharmaceuticals, making packaging choice a key focus for quality managers. Consider the following when evaluating your packaging solutions:
- High-Quality Insulation Materials: Effective packaging solutions should use high-quality insulation materials to reduce heat transfer and maintain temperature stability. These solutions should have undergone rigorous testing to ensure that the required temperature range can be maintained under real-world conditions, offering reliability and consistency while minimizing performance variability.
- Temperature Monitoring: Packaging that has integrated temperature monitoring systems, such as data loggers and real-time sensors, allows for immediate corrective actions if unexpected events occur.
- Durability: Packaging should be made of durable materials that protect against physical damage, tampering, or contamination during transit.
- Sustainability: Opt for environmentally friendly packaging solutions that align with your company’s sustainability goals.
Carefully evaluating packaging options minimizes temperature excursion risks, an often-overlooked aspect of operational excellence.
4. Secure Freight Capacity for the Product Launch
Regulatory approval dates are often unknown in advance, making it essential to partner with logistics providers that can secure space for transporting your pharmaceuticals when they are ready to ship.
Some providers use block space agreements to ensure sufficient freight capacity for critical or large shipments. Securing freight capacity ensures that the product can be transported promptly upon approval, avoiding delays that could jeopardize the launch.
5. Evaluate Availability and Responsiveness of External Partners
- Beyond securing freight capacity, ensure that your external partners —forwarders, ground handlers, airlines, and packaging suppliers—can quickly respond to and resolve issues is they occur.
- Availability: Ensure partners can handle larger volumes if sales grow or if you decide to expand to new markets.
- Responsiveness: Evaluate partners ability to solve potential problems that may arise during the NPI process and that they have effective contingency plans in place.
Evaluating external partners’ availability and responsiveness is crucial for maintaining a smooth and efficient cold chain.
6. Ensure Adequate Training of Personnel
Pharmaceuticals are handled by multiple parties, making thorough training crucial, especially for temperature-sensitive products. Ensure all personnel, including tarmac ground handlers, are well-trained and follow procedures.
Human errors, not just technical issues, can break the cold chain. Adequate training ensures that all personnel involved in the cold chain are competent and capable of handling the product correctly to ensure patient safety.
7. Collaborate with Proactive Logistics and Service Providers
Logistics is not a core business area for most pharmaceutical companies. Partner with proactive logistics providers and packaging suppliers with experience, who offer expert advice, such as how to optimize your loads and how to manage complex tradelanes.
Collaborating with proactive logistics providers ensures that the NPI process is managed efficiently and effectively.
The importance of meticulous planning and execution of an NPI cannot be overstated. A failed NPI doesn’t just impact a company’s bottom line—it delays or denies access to life-saving treatments for patients. By following these seven steps, pharmaceutical manufacturers can overcome logistical complexities, maintain compliance, and achieve a smooth product launch, ultimately delivering life-saving medications to patients in need.
With 40 years of experience working with the world’s largest pharmaceutical companies, Envirotainer has the knowledge and expertise to support you. Contact us to discuss your requirements and learn how we can support your NPI journey and make a meaningful difference in patients’ lives.
Resources
1IQVIA Report: The Global Use of Medicines 2024: Outlook to 2028. https://www.iqvia.com/insights/the-iqvia-institute/reports-and-publications/reports/the-global-use-of-medicines-2024-outlook-to-2028.
Get in touch
We are here to support you 24/7 with our global customer service. For non-urgent inquiries, please email us at support@envirotainer.com or for urgent issues, call our Operations Center.
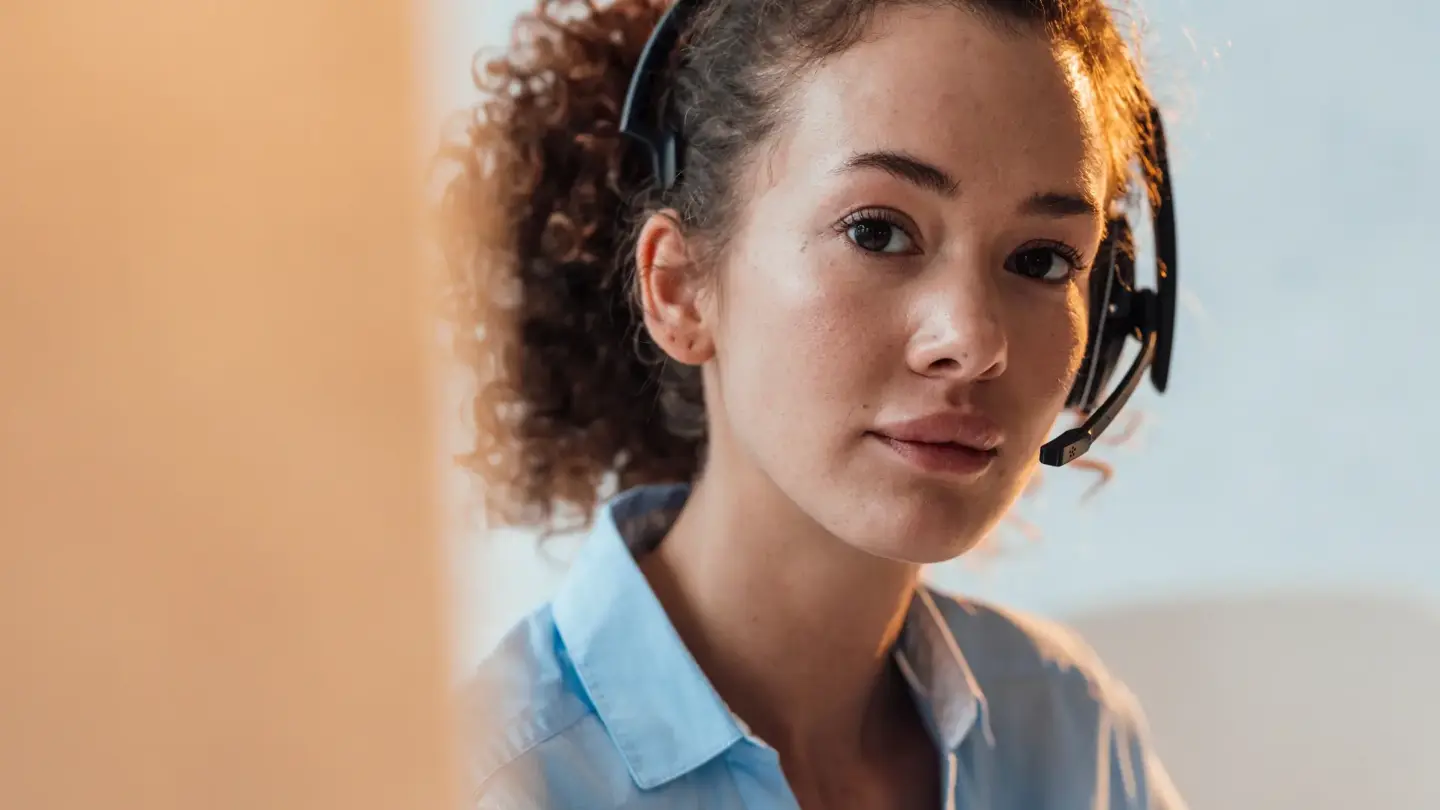