Reliability at stake: How to maintain 100% cold chain availability despite a pandemic
Sofia Wiwen-Nilsson
Head of Marketing and Communications
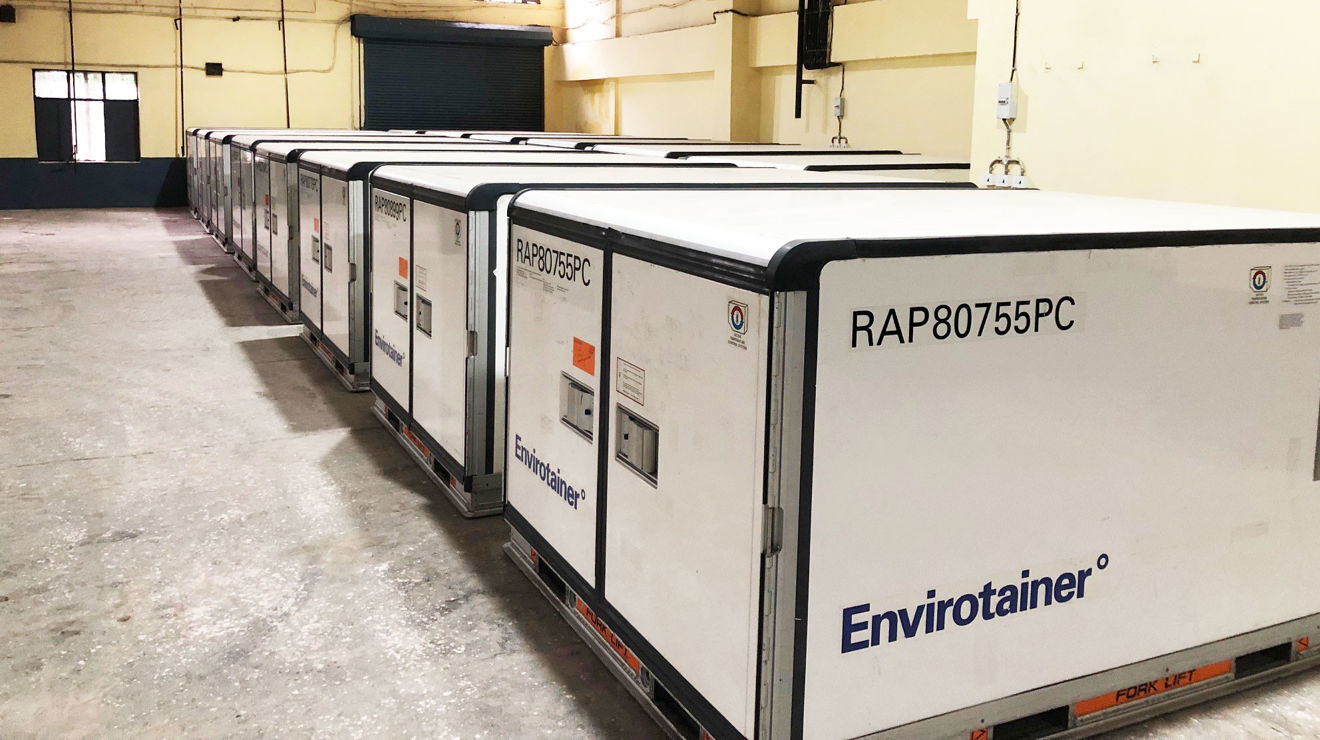
Having the largest cold chain container fleet for pharma in the world. Being an agile and data driven company. Implementing efficiency initiatives and novel ways of repositioning the container fleet. These are the main reasons why Envirotainer managed to offer 100% availability on all orders in 2020, despite a dramatic drop in global air freight capacity. Below, Niklas Adamsson, Chief Operating Officer at Envirotainer, explains how the company’s huge efforts to improve efficiency and capacity of their cold chain container services helped them deliver on top, despite the COVID-19 pandemic.
What were your biggest challenges in 2020 in terms of offering cold chain solutions?
2020 was a turbulent year. With the COVID-19 pandemic, the whole air freight industry was turned upside-down. Before the pandemic, about 50-60% of all air freight cargo was shipped on passenger flights. When a large share of passenger flights was cancelled in April, there was a huge capacity shortage for cold chain pharma logistics.
Our customers expect our cold chain containers to be reliable and always available
We have more than 50 service stations around the world, and it was a challenge to maintain our operational status with varying local, regional and national regulations and lockdowns. But we managed to receive all local permits necessary to be fully operational and keep our service level. We even opened up a number of new stations around the world to facilitate for our customers. They expect our active cold chain containers to be reliable and always available. Vital products in the form of temperature-sensitive medicines and vaccines are shipped in our containers.
Did you have to change your operations?
Return logistics became a huge challenge when a large share of air flight capacity disappeared. The cold chain supply chains we serve are not balanced; there are pharma clusters in certain regions and our airline customers do not want to return an empty container if they can take on paid cargo instead. So, we increased the number of one-way lease options with more than 120% in 2020.
Niklas Adamsson, Chief Operating Officer at Envirotainer
This means an increased logistic challenge for us regarding repositioning of containers, making sure that we have our assets in the right place at the right time ready for the next lease. Previously, much of the repositioning could be done by air, but with the capacity shortage we use ocean freight to a higher extent than before.
We managed to offer 100% availability in 2020 – and we had more than 50,000 shipments completed
The advantage of repositioning via ocean freight is a lower environmental footprint. The challenge is that our containers are tied up for several weeks on ships. I have 4-5 days planning horizon in my order book to make sure our active cold chain containers are available throughout the world to our customers. Despite that we managed to offer 100% availability in 2020 – and we had more than 50,000 shipments completed according to our customers’ demands.
How did you handle the pandemic internally in the organization?
While keeping our operational status and being available 24/7 we also had to take care of our employees and make sure they were safe and sound. All our customer service personnel started working from home and, luckily, we were ready for it. In the last couple of years, we have digitalized our customer service support systems by implementing a cloud-based Voice-over-IP phone system, global case management system and customer service through our customer portal. At the same time, all our stations have been open, and all our containers have been available to customers.
What do you think makes Envirotainer reliable in times of crisis?
First of all, we have the largest fleet of active containers in the industry, serving the world’s largest cold chain network with over 50 service stations, covering over 2,000 pharma trade lanes. We have lease agreements with over 100 airlines and all major international forwarders. This means we can be trusted and can deliver when others are unable. We did not miss a single customer order during 2020, even during the most devastating pandemic.
We have shipped more than 100 million COVID-19 vaccine doses to date – on top of our ordinary business
Our big fleet of containers implies a real buffer. We have shipped more than 100 million COVID-19 vaccine doses to date – on top of our ordinary business that is growing a lot. Pharma consumption went down a bit last year due to the pandemic so there is a backlog of pharma products that have to be shipped. There is a huge demand of our premium container RAP e2. We actually increased the number of RAP e2 containers in our fleet substantially in 2020 and will increase our capacity of that container further in 2021.
Container production at the Envirotainer Manufacturing and lab facilities in Sweden.
What other advantages do you have that helped you succeed in 2020?
We are very agile. We quickly managed to reorganize our operations in line with the new market conditions. In 2020 we even expanded our network of stations by opening several new stations in India and China. The newly opened station in Beijing quickly became a key hub for COVID-19 vaccine shipments. We have also improved the efficiency of our stations in the last years by implementing new system support, processes and methods, and we are reaping the fruits of it now. After each lease, it is vital that the containers are quickly available again for new leases. Thanks to our investments in efficiency, containers are serviced 50-60% faster than before. It is like F1 racing. When a container comes in, everyone knows what to do in terms of controls, service and repair. Agility is not only about logistics but also about having the right systems and people in place and to follow up service stations to find bottlenecks and to work with continuous improvements.
We use sophisticated machine learning and analytics to analyze the condition of the container so that we can always establish the reliability of each container to avoid temperature excursions
Moreover, we utilize data to a very high degree and work systematically with machine learning and analytics to improve our cold chain services. We register shipment and run time data of our containers continuously while being on a lease. This means we have in total 10 billion data points of actual shipment and run time data from our container fleet. We use sophisticated machine learning and analytics to analyze the condition of the container so that we can always establish the reliability of each container to avoid temperature excursions. The data is a true gold mine and has helped us keep temperature excursions to a minimum – less than 0.1%.