Releye® RLP – our latest innovation with an outstanding technology
Sofia Wiwen-Nilsson
Head of Marketing and Communications
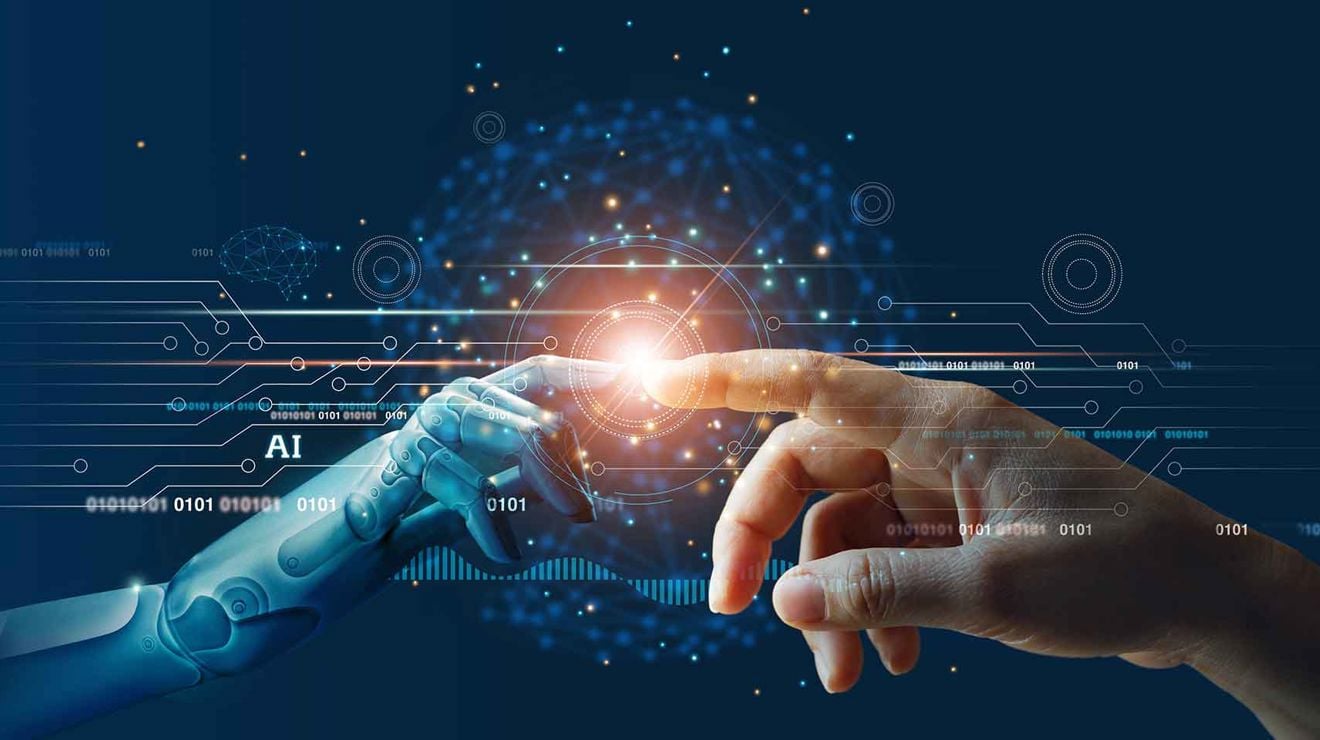
Releye® RLP, the latest temperature-controlled container from Envirotainer, introduces a new level of safety, real-time monitoring, and unsurpassed autonomy. Precious pharmaceuticals are protected up to 170 hours (more than a week) without recharging container batteries. In addition, independent temperature control systems provide redundancy on all critical container functions. But what technology supports this outstanding performance? Bernt Anderberg, Chief Technology Officer and Chief Supply Chain Officer at Envirotainer, explains.
What distinguishes Releye® RLP from your existing fleet of temperature-controlled containers?
We already have a fleet with the latest generation of containers, but we wanted to keep our market-leading position in terms of innovation, performance, and functionality. Our previous containers are excellent, but we constantly need to improve. So, we have worked on performance and have added features that can support our clients in the future.
We set out to make the world’s best temperature-controlled container – again. With that said, we want to set the pace and take the lead, both commercially and technologically.
Releye® RLP is equipped with many sensors so that you can monitor an array of aspects in real-time. What kind of sensors are there?
We have a total of 18 sensors that monitor important aspects during shipping, including eight sensors for temperature in different places in and outside the cargo space: humidity, circuit boards, door openings, battery status, cargo loaded, and GPS.
An air curtain protects the cargo from temperature deviations when doors are opened temporarily, for example, at customs inspections. We also measure position via GPS.
The sensors collect data continuously, and the data is uploaded every five minutes to be available at the customer portal.
Releye® RLP has redundancy on all critical functions. What does that imply for performance and safety?
It’s critical for our clients that their cargo is protected from temperature deviations, no matter what happens during shipping. Therefore, we have three refrigeration modules that work independently of each other. If one or two are switched off for any reason, the others continue to work.
The same applies to our four battery systems that function independently of each other. If one goes down, battery life will be shortened, but you will receive an alarm that you must recharge earlier.
The redundancy adds an extra safety level in the unlikely case there would be problems with functionality. We have designed a fault-tolerant system with a very high-security level. Even if you were to lose all communication with the container, the modules themselves will be able to continue to operate and to measure the temperature locally. We already have a certain redundancy in our existing fleet, but this is full redundancy in all main systems. The data is uploaded every five minutes to be available at the customer portal so that our clients can follow the status of the container for every five-minute interval.
What has been the biggest challenge when developing Releye® RLP?
It’s an advanced system. We have developed Releye® RLP in collaboration with our clients and have based the requirements on their needs. It’s not just a container but a whole service system that must be connected and aligned.
We have developed Releye® RLP in collaboration with our clients and have based the requirements on their needs
Besides the technical solution we are also introducing a new size, a three-pallet size, that is a novelty on the market. The load capacity, about the external dimensions, is incredibly optimized. We have the largest load height as well as the largest internal dimensions for an active container of this size, thanks to modern, high-performance materials. This has enabled us to have thin walls in combination with accurate temperature control.
Another challenge has been to find the optimal balance between autonomy, weight, and durability. We could have increased the autonomy even more than our unsurpassed 170 hours, but that would have increased the weight and an even longer autonomy had not been so relevant for our clients. Durability is important as we are providing sustainable solutions with reusable containers, but you also want a state-of-the-art insulation for the safest possible temperature-controlled shipments. There has been a lot of calculations in the development phase to balance all these aspects to arrive at a solution that best serves our clients.
Bernt Anderberg, Chief Technology Officer and Chief Supply Chain Officer
What are you most proud of?
We have developed a container with fantastic performance and accuracy together with a functionality that is relevant to our clients. It’s simply a great temperature-controlled container that is sustainable over time.