All hands on deck
Mattias Isaksson
Head of Marketing & Communications
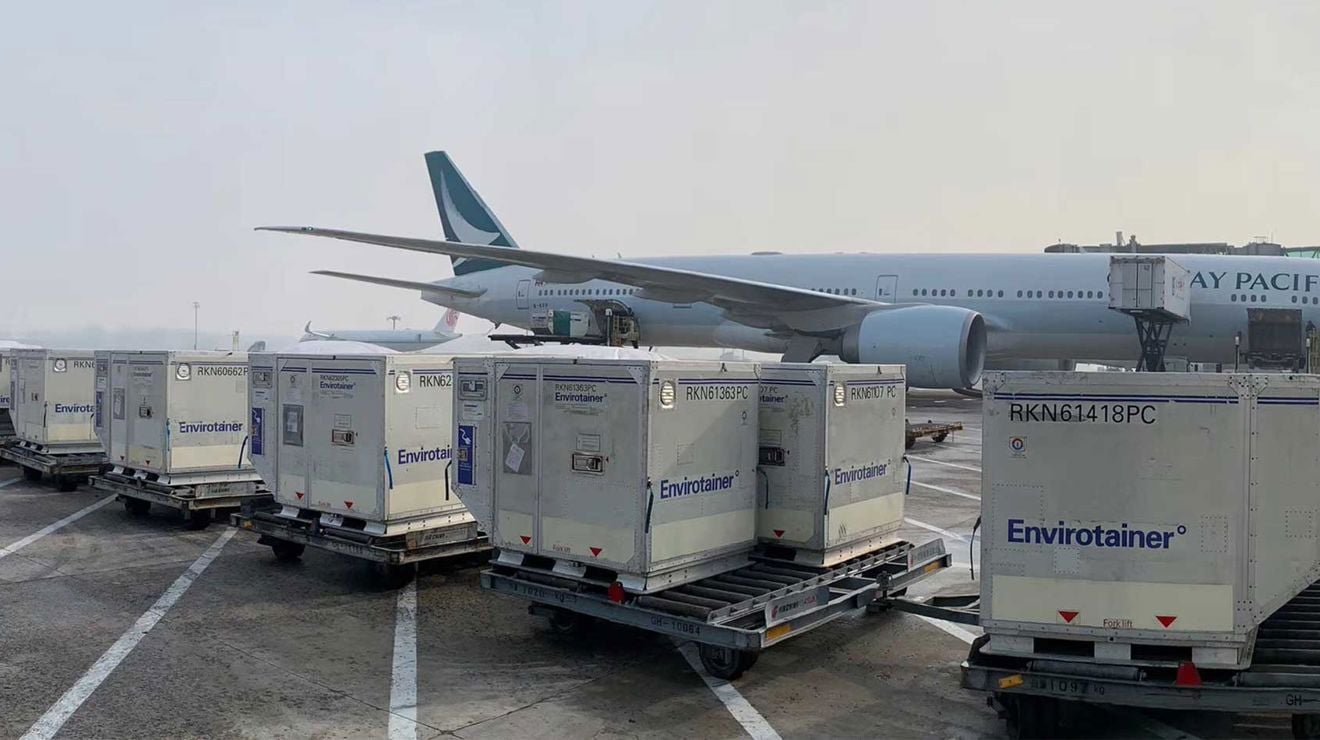
Even the best laid plans can be upended. This is what happened a couple of weeks ago for a pharmaceutical company that was planning to ship a large amount of API (Active Pharmaceutical Ingredient) that was needed to develop a batch of anti-infection medicine. Even with a short lead-time of five (5) days, Envirotainer came through and provided 22 RKN e1’s out of Hong Kong and Shanghai for the shipment from Beijing to New York.
China is the biggest API exporter in the world and play a key role in providing high-quality API’s to the global pharmaceutical supply chain. Many of these API products are high-value and temperature sensitive. The API in question required to be kept within a strict 2-8 degrees Celsius during the entire shipment. When the original shipment plans fell through, it became critical to quickly find a secure and efficient way of moving the large volume of temperature sensitive API. Envirotainer is the only solution provider in the world that has the partner network, availability of active temperature-controlled units and the competence to handle massive volumes on such a short notice. Especially during peak-season for air cargo when cargo space on airplanes becomes limited.
Jeff Su, Envirotainer’s Strategic Account Manager in China explains, “We’ve been investing heavily in our capabilities in China over the past years, adding both competence and station capacity which really helped the pharmaceutical company. We’ve been training our local partners on how to best handle temperature-sensitive medicines and we’ve also added more customer support resources in the Asia-Pacific region to provide hands-on technical support when needed.” He continued, “We also have fantastic partners in Cathay Pacific and Air China who really came through and shipped these 22 RKN e1’s during 2-3 days from Hong Kong and Shanghai to Beijing to load the API and then onwards to JFK airport in the US. Really well done!”
All API arrived safely into the hands of the CMO (Contract Manufacturing Organization) in the New York area, on time and in the right condition. The process of manufacturing the anti-infection medicine can now proceed as originally planned.